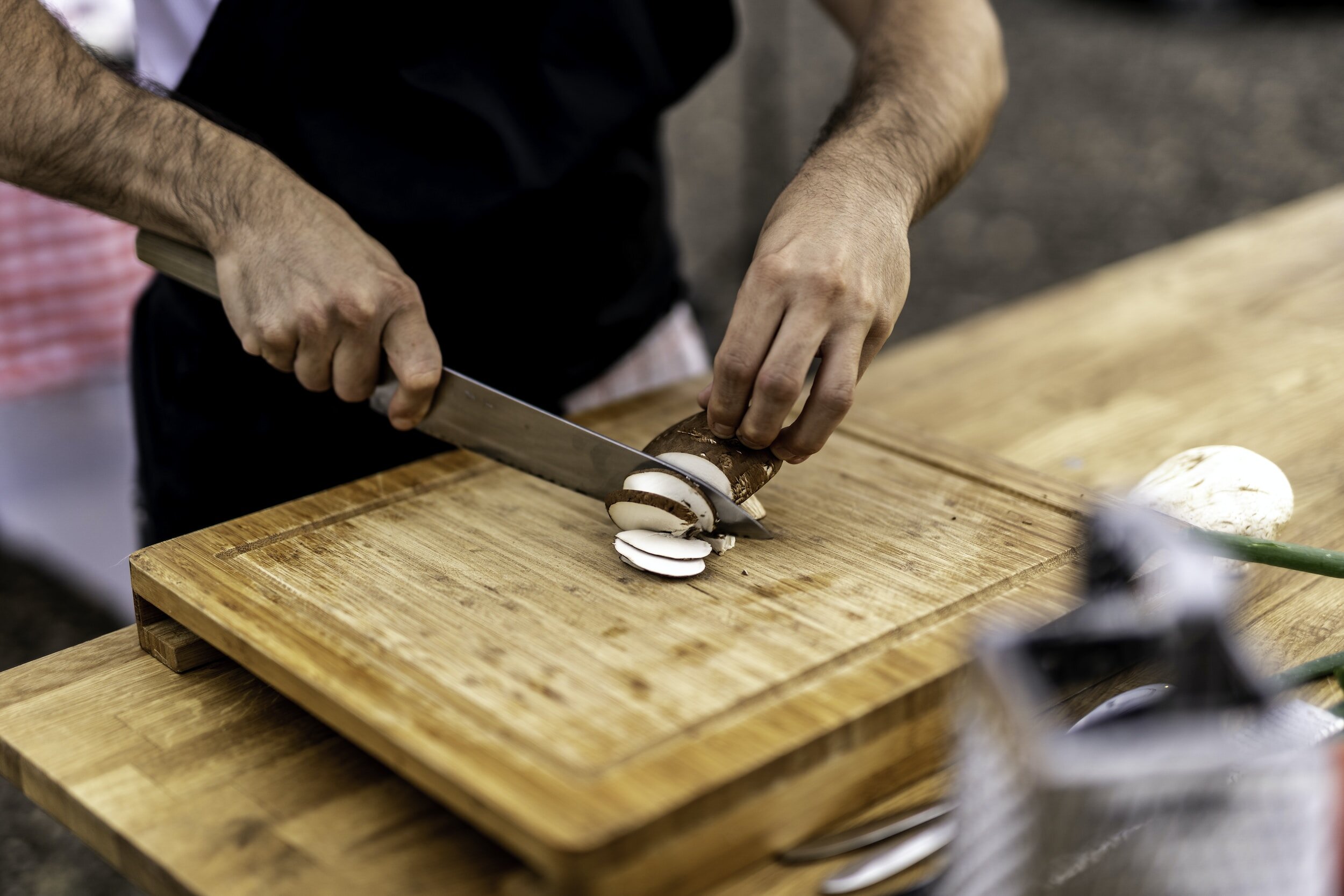
assistive *manual* kitchen food slicer
Design rules & Constraints
Design a slicer to fit in a 10in x 7in x 7in box.
Input is a manual crank rotation.
The feeding is passive, using gravity.
Include a visually appealing linkage mechanism.
Use a straight blade, no circular blades allowed.
Blade motion shouldn't be a full rotation.
Accommodate vegetables/fruits up to 2 inches.
Prototype with a plastic blade.
Evaluate by cutting a banana.
Our Human-Centered Design (HCD) focuses on creating a fruit slicer for those with hand tremors. The design prioritizes safety, ease of use, and replicating a standard cooking experience. Our successful prototype offers an intuitive, simple, and safe chopping mechanism for enhanced independence and improved quality of life.
The mechanism comprises four links: Ground, crank, L-shaped coupler, and blade rocker. Link lengths are measured as 135 mm (ground), 45 mm (crank), 53.24 mm (coupler), and 129.17 mm (rocker). The mechanism is a four-bar Grashof Class 1 with one degree of freedom to control motion with high level of accuracy. Change points occur when the crank and coupler align collinearly at 0° and 180°, corresponding to toggle positions. Inversions were attempted, but intense rotational motion caused issues. The full rotation guides the knife in an oscillatory motion to mimic a natural cutting motion. Instantaneous centers reveal key information about the direction and velocity of moving links. Understanding instantaneous centers aids in analyzing the mechanism's velocities, essential for an engineer's assessment.
assistive *automatic* kitchen food slicer
Design rules & Constraints
Design a slicer to fit in a 10in x 12in x 12in box.
Input is a 12 V brushed DC motor.
No hands feeding— utilize a feeding mechanism.
Hands off after switch is flipped.
Include a visually appealing linkage mechanism.
Use a straight blade, no circular blades allowed.
Blade motion shouldn't be a full rotation.
Accommodate vegetables/fruits up to 2 inches.
Prototype with a plastic blade.
Evaluate by cutting a banana.
Complex Gear Reduction System
Non-Grashof Linkage System
Rack and Pinion Feeding Mechanism
The blade is secured by a bracket, forming a four-bar non-Grashof linkage system with a dyad driver for oscillating movement between two toggle positions. In a three-linkage system, the blade, arc blade bracket, and a single link from the four-bar system work together. As the dyad driver rotates, the blade undergoes a continuous arcing motion, influenced by a quick-return mechanism with a 1:2 ratio.
The feeding mechanism involves a cutting board connected to a motor-driven geneva mechanism, controlling a rack and pinion system. The geneva mechanism ensures the food remains stationary during chopping, using intermittent rotary motion. After chopping, the geneva drive moves the cutting board forward, preparing the food for the next slice. This cycle repeats until completion or the cutting board reaches its final position.
While the CAD model showcases an efficiently designed motor-powered fruit slicer, practical assembly may reveal unforeseen issues. The current mechanical advantage is suboptimal. Future iterations include plans to lengthen the dyad driver and adjust the linkage. To address potential vibration, drilling holes for screws to secure major components into the wooden base is under consideration. Additionally, friction-related challenges with sliding mechanisms against plastic components necessitate thorough sanding and minimizing contact points for smooth motion. The system's longevity depends on the motor's optimal performance, prompting potential adjustments to the force it provides as it degrades over time or encounters increased loads or battery drain.
Upon testing, was a successful design. Chopped three clean slices of banana, and further testing will be done on harder food materials to ensure adaptability and wide usage.